Categorías: Hechos interesantes, Electricista de automóviles
Cantidad de vistas: 31242
Comentarios sobre el artículo: 0
Recuperación de energía eléctrica y su uso.
La forma tradicional de deshacerse del exceso de energía liberada en convertidores de frecuencia Durante el frenado de los motores asíncronos controlados por ellos, se disipaba en forma de calor en las resistencias. Las resistencias de frenado se usaron donde había una alta inercia de la carga, por ejemplo, en centrífugas, en vehículos eléctricos, en soportes de carga, etc.
Tal solución era necesaria para limitar la tensión máxima en los terminales de los convertidores en modo de frenado. De lo contrario, los convertidores de frecuencia fallarían, porque sería imposible controlar los parámetros de aceleración y frenado.
Las resistencias de frenado no cargaban económicamente el equipo, pero siempre entrañaban algunos inconvenientes. Las resistencias son dimensionales, están muy calientes, necesitan protección contra la humedad y el polvo. Y todo esto está relacionado solo con el hecho de que es necesario disipar la energía desperdiciada, para lo cual la empresa paga dinero, y el dinero no es pequeño, especialmente si estamos hablando de producción a gran escala.
En el verano, el calentamiento adicional del aire circundante es especialmente indeseable, porque el equipo tecnológico ya se calienta con aire caliente, y luego también hay resistencias calentadas a 100 grados y más. Necesita ventilación adicional - nuevamente costos.
Pero hay otra forma. ¿Por qué disipar energía en vano? Puede devolverlo a la red y así ahorrar energía. Luego vienen al rescate sistemas de recuperación de energía.
Por supuesto, los convertidores de frecuencia actuales reducen en gran medida el consumo de electricidad de los equipos, debido a la optimización del suministro de energía de los motores de diversos equipos tecnológicos, y esto ahorra recursos. Pero el uso de la recuperación aumenta aún más los ahorros. Las resistencias no pueden disipar la energía durante el frenado, pero pueden devolverse a la red teniendo en cuenta los parámetros actuales de la red.
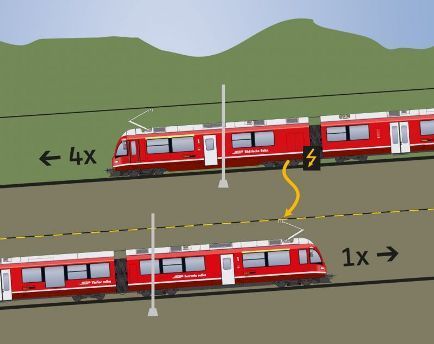
Hoy, los principales fabricantes de maquinaria y equipos industriales ya están introduciendo estos sistemas en vehículos eléctricos: para trolebuses, trenes eléctricos, escaleras mecánicas, tranvías y, finalmente, para automóviles eléctricos.
¿Cómo funciona el sistema de recuperación? Una fuente de corriente alterna que suministre un motor u otra instalación debe poder recuperar la energía. Para esto, en lugar de un rectificador convencional, se utiliza un convertidor modulado por ancho de pulso. Tal convertidor puede dirigir flujos de energía tanto de una fuente a un consumidor como de un consumidor a una fuente. De esta manera le permite llevar el factor de potencia a la unidad.
Una cascada IGBT típica del convertidor de frecuencia que funciona en el modo de recuperación se representa inicialmente como un rectificador de corriente sinusoidal, pero al frenar genera una señal modulada por ancho de pulso, en la que la dirección de la corriente, cuando el voltaje en los terminales está por encima de cierto nivel, no se dirige desde la red, y a la red desde el circuito del consumidor.
La diferencia de voltaje entre la red de suministro y el circuito de carga se aplica al inductor de recuperación. La inductancia bloquea los armónicos de alta frecuencia, y se obtiene una corriente sinusoidal casi pura, no hay necesidad de equipos de sincronización, es suficiente aplicar tres pulsos de prueba desde el modulador PWM a la red para determinar la frecuencia y fase del voltaje en el momento actual.
Un ejemplo son los convertidores de frecuencia con un sistema de recuperación de Control Techniques, que se utilizan, en particular, en las fábricas de Lamborghini y Nissan para alimentar bancos de prueba dinámicos, así como en escaleras mecánicas y diversas soluciones metalúrgicas.
La esencia es la misma en todas partes: Se crea un flujo de energía bidireccional para el consumidor desde la red, desde la fuente y desde el consumidor hasta la red. Al diseñar sistemas de recuperación, se tienen en cuenta una serie de factores: rango de voltaje de la red, clasificación del equipo y factor de potencia, potencia máxima teniendo en cuenta la sobrecarga, nivel de pérdidas.
El diagrama que se muestra en la figura muestra una solución de un solo motor, donde la unidad del motor y la unidad del recuperador están cada una en una copia, sus valores son iguales. Pero a veces se producen sobrecargas del motor, y luego se requiere una unidad de recuperación más potente para cubrir el límite de voltaje más bajo y las pérdidas del motor.
El mismo principio garantiza el funcionamiento de varios motores con varios accionamientos de motor, al tiempo que pone un potente accionamiento de recuperación que puede pasar por la potencia total de todos los motores del sistema, teniendo en cuenta la posibilidad de frenado simultáneo de todos los motores.
Para limitar la corriente de arranque en sistemas con varios motores, cuando se combinan los buses de CC, se utilizan módulos de tiristores, conectados por contactores a los condensadores del convertidor cargados por CC. Después de cargar los condensadores, el módulo de tiristores se apaga. Obviamente, los sistemas de recuperación están configurados de manera diferente y están diseñados individualmente.
Hablando de recuperación, uno no puede evitar recordar los sistemas de frenado regenerativo utilizados en los motores de automóviles híbridos modernos, donde la base es el camino de la recuperación eléctrica de la energía cinética.
Cada vez que un automóvil se mueve, se manifiesta energía cinética. Pero cuando se frena de la manera tradicional, el exceso de energía simplemente se pierde en forma de calor, las pastillas de freno rozan los discos de freno, desperdiciando energía cinética en vano, calentando material de fricción y metal, y finalmente perdiendo calor al aire circundante. Este es un enfoque muy derrochador.
El sistema de frenado regenerativo no consume energía cinética simplemente por fricción para frenar. En cambio, se utiliza un motor eléctrico incluido en la transmisión, que comienza a actuar como generador durante el frenado, convirtiendo el par en el eje a electricidad cargando la batería, y el par de frenado del rotor que surge en el modo generador le da al automóvil el frenado deseado. La energía almacenada en la batería de esta manera después de algún tiempo nuevamente sirve para mover el automóvil, es decir, se reutiliza.
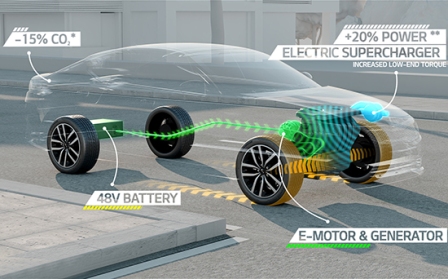
El frenado regenerativo le permite maximizar el uso de los recursos disponibles de cada carga de batería, y se ahorra mucho combustible. Dado que durante el frenado, el 70% de la energía cinética está en el eje delantero, el sistema de recuperación está montado en el eje delantero para ahorrar energía de manera más eficiente.
La mayor eficiencia del frenado regenerativo se logra a altas velocidades, y a bajas velocidades, la eficiencia del sistema disminuye. Por esta razón, junto con el frenado regenerativo, de una forma u otra, está presente un sistema de freno de fricción. El trabajo conjunto de los dos sistemas es proporcionado por un controlador electrónico.
El controlador implementa una serie de funciones: controla la velocidad de rotación de las ruedas, mantiene el par de frenado correcto, distribuye la fuerza de frenado entre los frenos de recuperación y fricción, y mantiene un par que es aceptable para una carga óptima de la batería.
Por supuesto, no existe una conexión mecánica directa entre el pedal del freno y las pastillas de fricción en tales vehículos. La unidad electrónica garantiza la interacción correcta del ABS, el sistema de estabilidad del tipo de cambio, el sistema de distribución de la fuerza de frenado y el refuerzo de freno de emergencia.
Ver también en electro-es.tomathouse.com
: