Categorías: Como funciona
Cantidad de vistas: 23713
Comentarios sobre el artículo: 1
Cómo se organiza y funciona la máquina de soldadura por plasma
El plasma en física es el cuarto estado de la materia después de las formas sólidas, líquidas y gaseosas, cuando la ionización parcial o completa del medio a partir de moléculas y átomos previamente neutros ocurre bajo la condición de cuasineutralidad: la densidad de volumen de todas las partículas cargadas es igual.
En la tecnología de soldadura, se utilizan las siguientes propiedades del plasma a baja temperatura (menos de un millón de grados Kelvin):
-
muy alta conductividad eléctrica;
-
la fuerte influencia de los campos magnéticos externos en el flujo de corrientes en él, contribuyendo a la formación de chorros y capas;
-
manifestación de efectos colectivos, expresados por el predominio de fuerzas magnéticas y eléctricas sobre gravitacionales.
Principios para crear y operar antorchas de plasma
En este método de soldadura, la fuente de calentamiento de metales hasta el punto de fusión es un arco de plasma de gas ionizado, que se dirige en la dirección correcta. Es producido por un dispositivo especial llamado plasmatron o antorcha de plasma.
Clasificación por tipo de arco
Por el principio de funcionamiento, el plasmatrón puede ser de acción directa o indirecta.
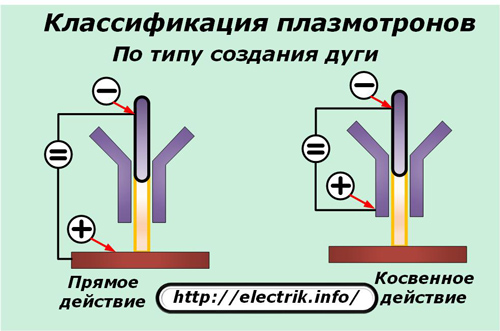
En el primer caso, la diferencia de potencial del campo externo del generador, creando las condiciones para la formación de un arco, se aplica directamente a la pieza de trabajo y al electrodo del quemador de gas. Debido a esto, se incrementa la eficiencia de enfriamiento de la estructura.
En el segundo método, el voltaje eléctrico se aplica solo entre las partes del quemador para crear un chorro de plasma. Debido a esto, es necesario complicar el sistema de enfriamiento del conjunto de boquilla.
Para los plasmatrones de acción directa, se produce un arco que se asemeja aproximadamente a una forma cilíndrica, expandiéndose ligeramente en la superficie del metal que se procesa.
Dentro de la boquilla eléctrica neutra, se produce compresión y estabilización del arco. En este caso, la combinación de la energía térmica y cinética del plasma forma una mayor potencia, lo que permite que el metal se derrita más profundamente.
Los quemadores indirectos crean un plasma en forma de chorro cónico rodeado por una antorcha dirigida hacia el producto. El chorro es expulsado por la corriente de plasma que sale del quemador.

Clasificación de los métodos de enfriamiento del quemador.
Debido a la alta temperatura del plasma, se utilizan varios métodos para enfriar los detalles de la antorcha de plasma:
-
soplando aire;
-
eliminación de calor debido a la circulación forzada de agua.
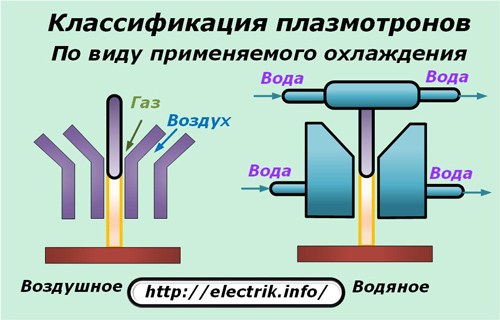
La refrigeración por aire es menos costosa, y la refrigeración líquida es la más eficiente, pero compleja.
Clasificación de los métodos de estabilización de arco.
El quemador de gas debe proporcionar una columna de temperatura uniforme, estable en magnitud y dirección con su estricta fijación a lo largo del eje de la boquilla y el electrodo.
Para este fin, se han desarrollado tres tipos de diseños de boquillas que utilizan energía:
1. gas;
2. agua;
3. campo magnético.
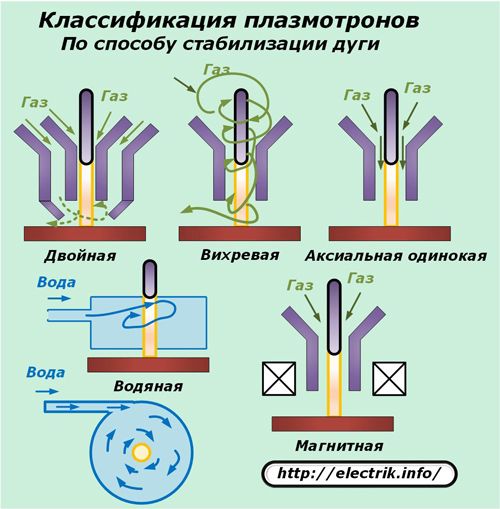
En el primer método Una corriente fría de gas, que sopla una columna de plasma, la enfría y la comprime simultáneamente. Dependiendo de la dirección de la corriente de gas, se crea la estabilización:
1. axial - con soplado paralelo de la columna;
2. girando cuando el flujo de gas se crea en la dirección perpendicular.
El segundo método comprime el arco de manera más eficiente y se utiliza en plasmatrones utilizados para la deposición o corte de metales.
La estabilización axial es más adecuada para soldar y revestir metales.
El esquema de doble estabilización combina las características de axial y vórtice. Al usarlo, es posible pasar gas de tres maneras:
-
solo a través del canal central principal;
-
a través de ambos;
-
exclusivamente a través de externos.
Cada método crea diferentes esquemas para comprimir la columna de plasma.
Estabilización de agua utiliza flujos de fluidos contrarrevolucionarios.El vapor generado en este proceso ayuda a crear plasma con una columna que se calienta hasta 50 mil grados en la escala Kelvin.
Un inconveniente significativo de este método es la intensa combustión del cátodo. Para tales dispositivos, el electrodo está hecho de grafito, desarrollando mecanismos para su aproximación automática a la pieza de trabajo a medida que la longitud se consume continuamente.
Se observan dispositivos de antorcha de plasma estabilizados con agua:
-
complejidad de diseño;
-
baja confiabilidad del sistema de alimentación de electrodos;
-
La complejidad de los métodos de excitación del arco.
Estabilización magnética Funciona debido al campo magnético direccional ubicado a través del movimiento de la columna de arco. Su eficiencia es la más baja, y el solenoide integrado en la boquilla complica enormemente el circuito de la antorcha de plasma.
Sin embargo, la estabilización magnética se usa para impartir movimiento de rotación al punto anódico dentro de las paredes de la boquilla. Esto permite reducir la erosión del material de la boquilla, lo que afecta la pureza del chorro de plasma.
Todas las construcciones de plasmatrones consideradas anteriormente son de arco. Pero hay otro tipo de dispositivos similares de generación de plasma debido a la energía de la corriente de alta frecuencia que pasa a través de la bobina inductora. Tales plasmatrones se llaman inducción (HF) y no requieren electrodos para crear una descarga de arco.
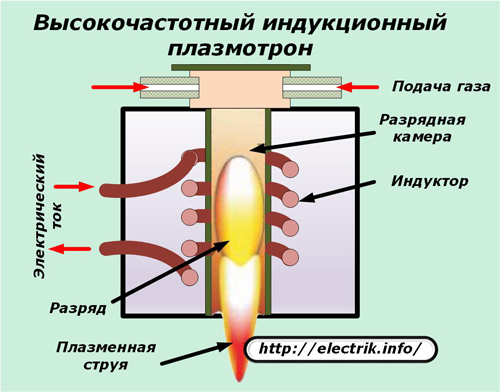
No tienen ventajas especiales para influir en los metales procesados en comparación con los dispositivos de arco y se utilizan para resolver procesos tecnológicos individuales, por ejemplo, la producción de metales en polvo puros.
Características de diseño de quemadores.
El funcionamiento de uno de los tipos de antorchas de plasma puede explicarse en la siguiente figura.
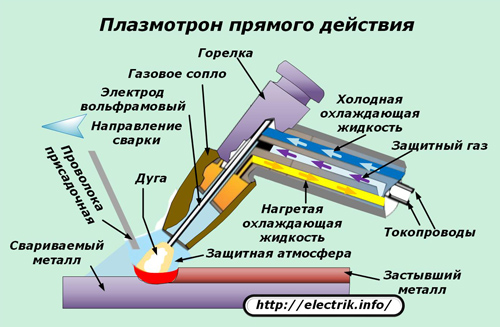
El arco de plasma durante la soldadura se crea dentro de la cubierta atmosférica protectora formada al suministrar gas inyectado al área de trabajo. Con mayor frecuencia eligen argón.
El gas formador de plasma (fuente de ionización) puede funcionar:
-
argón
-
nitrógeno
-
helio
-
aire
-
hidrógeno;
-
mezclas de los gases listados.
Tenga en cuenta las características de su funcionamiento:
-
el hidrógeno es explosivo;
-
los nitruros y el ozono se liberan del aire;
-
helio querido;
-
El nitrógeno a altas temperaturas afecta el medio ambiente.
El tungsteno se elige con mayor frecuencia como material para los electrodos debido a las propiedades mecánicas más adecuadas y la resistencia a las altas temperaturas.
La boquilla de gas se fija en el quemador y se sopla con una corriente protectora. Se bombea fluido frío a lo largo de las líneas hidráulicas y se descarga el calor.
Los cables que transportan corriente suministran energía eléctrica de corriente continua o alterna a los electrodos.
Para alimentar el arco formador de plasma, se conecta una fuente de corriente con un voltaje de aproximadamente 120 voltios para soldar y aproximadamente 300 en reposo, para cortar.
Dispositivo generador de plasma
Se puede usar corriente alterna o corriente continua para iniciar el plasmatron. Como ejemplo, considere la operación de un generador de red de suministro de energía convencional 220 voltios.
La resistencia de lastre limita la corriente de alimentación. El acelerador controla la carga. El puente de diodos convierte una tensión alterna para mantener un arco de trabajo.
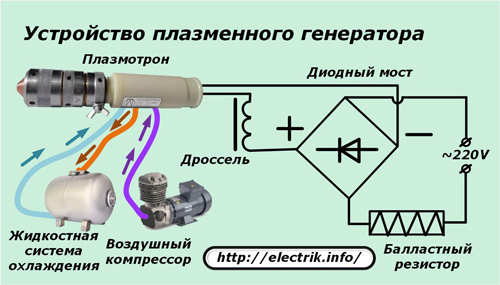
Un compresor de aire suministra gas protector al quemador, y un sistema de enfriamiento hidráulico hace circular el fluido en las líneas de plasma para mantener una eliminación efectiva del calor.
Técnica para corte y soldadura por plasma.
Para encender y mantener el arco de soldadura, se utiliza energía de corriente eléctrica y, para su excitación sin contacto, un oscilador (fuente de oscilación).
El uso de un arco piloto entre el electrodo y la boquilla puede facilitar significativamente el proceso de iniciar el plasma.
Dicha soldadura permitirá unir casi todos los metales y aleaciones ubicados en el plano inferior o vertical.
Sin preprocesar los bordes, los biseles con un grosor de hasta 15 mm se pueden soldar a biseles.En este caso, se forma una penetración característica con formas específicas debido a la salida del chorro de plasma más allá de la parte posterior de la parte soldada a través de las ranuras pasantes.
De hecho, la soldadura por plasma en la mayoría de los casos es un proceso doblemente continuo:
-
cortar a través del material de la pieza de trabajo;
-
sitio de soldadura cortado.
La tecnología de corte se basa en:
-
capa de metal fundido en el sitio de tratamiento;
-
soplando la fracción líquida en la corriente de plasma.
El grosor del metal afecta la tecnología de corte. Para productos delgados, se utiliza el método indirecto del arco, y para los más gruesos, las antorchas de plasma conectadas directamente funcionan mejor.
El corte por plasma es el más económico para todos los metales, incluido el acero al carbono.
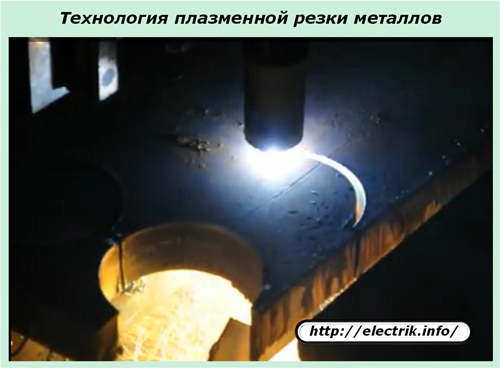
Para realizar soldadura y corte por plasma, se han desarrollado líneas automatizadas e instalaciones manuales.
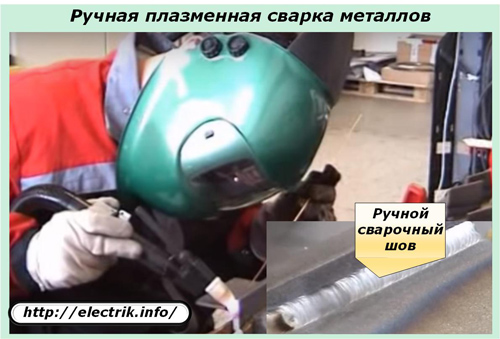
Tipos de soldadura por plasma.
El poder de la corriente aplicada afecta el poder del arco creado. Su tamaño determina tres tipos de soldadura:
1. microplasma;
2. promedio;
3. a altas corrientes.
Soldadura por microplasma
Funciona con corrientes limitadas a 0.1 ÷ 25 amperios. Esta tecnología se utiliza en electrónica, instrumentación, joyería, fabricación de fuelles, membranas, termopar, papel de aluminio, tubos y contenedores de paredes delgadas, lo que le permite conectar firmemente piezas con un grosor de 0.2 ÷ 5 mm.
Para procesar diferentes materiales, se seleccionan combinaciones de gases formadores de plasma y gases protectores, el grado de compresión del arco y la proximidad al ánodo. Al procesar materiales especialmente delgados, el modo de pulso se usa para el suministro de arco de bajo amperaje con el suministro de pulsos de corriente bipolar.
Durante el paso de un pulso de una polaridad, el metal se deposita o suelda, y cuando se detiene debido a un cambio de dirección, el metal se enfría y cristaliza, y se crea un punto de soldadura. Para su buena educación, se optimiza el proceso de suministro de corriente y pausa. En combinación con el control de amplitud y la extracción de electrodos, esto permite lograr compuestos de alta calidad de diversos metales y aleaciones.
Para realizar la soldadura por microplasma, se han desarrollado muchas tecnologías que tienen en cuenta diferentes ángulos de inclinación de las antorchas de plasma, creando vibraciones transversales para destruir las capas de óxido, moviendo la boquilla en relación con la soldadura que se está procesando y otros métodos.
Soldadura por plasma a corrientes medias de 50 ÷ 150 amperios utilizado en producción industrial, ingeniería mecánica y reparación.
Altas corrientes desde 150 amperios se utilizan para soldaduras por plasma, llevando a cabo en condiciones industriales el procesamiento de aceros aleados y con bajo contenido de carbono, aleaciones de cobre, titanio, aluminio. Le permite reducir el costo de los filos de corte, aumentar la productividad del proceso, optimizar la calidad de las costuras en comparación con los métodos de arco eléctrico de las juntas.
Superficie de plasma de metal y pulverización de superficie
Las piezas individuales de la máquina requieren la provisión de superficies de alta resistencia o resistentes a altas temperaturas o ambientes agresivos. Con este fin, se recubren con una capa protectora de metal costoso mediante métodos de tratamiento con plasma. Para hacer esto, el alambre o polvo preparado en pequeños gránulos se introduce en la corriente de plasma y se rocía en estado fundido sobre la superficie a tratar.
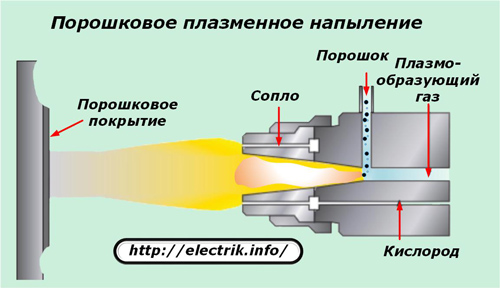
Ventajas de este método:
-
la capacidad del plasma para fundir cualquier metal;
-
la capacidad de obtener aleaciones de diferentes composiciones y crear recubrimientos multicapa;
-
la disponibilidad de formularios de procesamiento de cualquier tamaño;
-
conveniencia de ajustar las características energéticas de los procesos.
Ventajas de la soldadura por plasma
La fuente de arco creada por la soldadura por plasma difiere de la eléctrica convencional:
1. un área de contacto más pequeña en el metal tratado;
2. mayor efecto térmico debido al acercamiento a una forma cilíndrica;
3. aumento de la presión mecánica del chorro sobre el metal (aproximadamente 6 ÷ 10 veces);
4. La capacidad de mantener la combustión del arco a bajas corrientes, hasta 0.2 amperios.
Por estas cuatro razones, la soldadura por plasma se considera más prometedora y multipropósito en el procesamiento de metales. Proporciona una mejor fusión dentro de un volumen reducido.
El arco de plasma tiene la concentración de temperatura más alta y le permite cortar y soldar metales de mayor espesor incluso con ciertos aumentos en la distancia desde la boquilla del quemador hasta la pieza de trabajo.
Además, los dispositivos de soldadura por plasma difieren:
-
dimensiones relativamente pequeñas;
-
fiabilidad en el trabajo;
-
simplicidad de la regulación del poder;
-
inicio fácil
-
Terminación rápida del modo de funcionamiento.
Desventajas
El alto costo de los equipos limita la introducción generalizada de la soldadura por plasma en todas las industrias y entre las pequeñas empresas.
Ver también en electro-es.tomathouse.com
: